Sin muelas abrasivas, no hay rectificado. Desempeñan un papel crucial en la obtención de acabados precisos y en la eliminación de material en piezas metálicas. Su elección adecuada depende de varios factores, como el material de la pieza, la velocidad de corte y el tipo de rectificado.
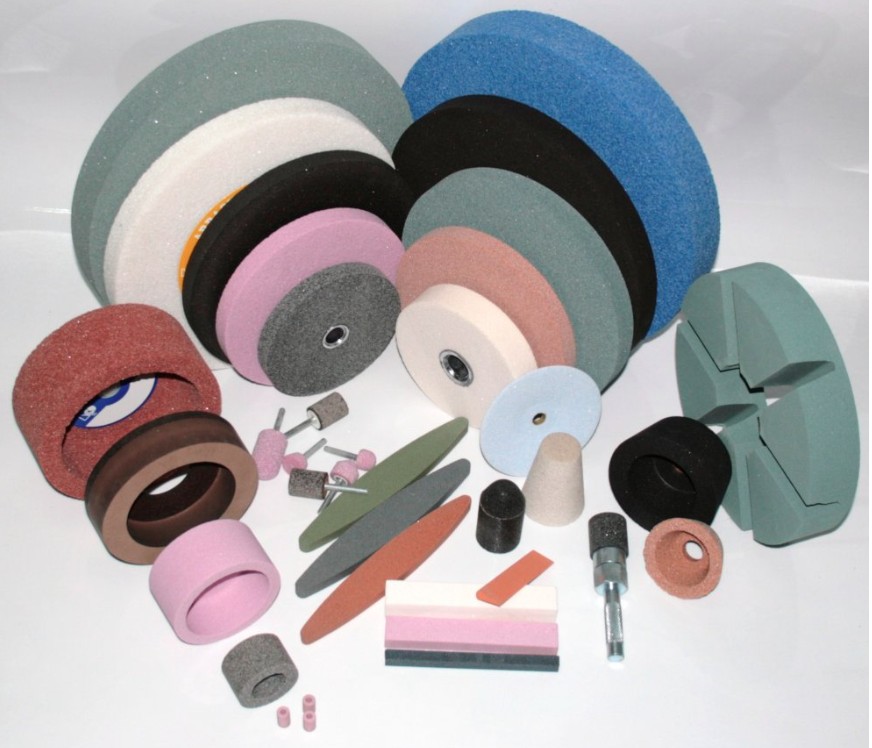
1. Composición de las muelas abrasivas
Las muelas se componen principalmente de granos abrasivos y un aglutinante, aunque existen pequeños huecos entre ellos.
Los materiales abrasivos más comunes incluyen:
CONVENCIONALES:
- Óxido de aluminio (Al₂O₃): Ideal para aceros de alta resistencia y materiales ferrosos.
- Carburo de silicio (SiC): Adecuado para materiales no ferrosos y aleaciones duras.
SUPERABRASIVOS:
- Nitruro de boro cúbico (CBN): Para el rectificado a alta velocidad de férricos de alta dureza y aleaciones termorresistentes. Según la norma FEPA (Federación Europea de Productores de Abrasivos) se designa con el prefijo B.
- Diamante: Principalmente empleado en la rectificación de cerámicos y materiales ultra duros. Según la norma FEPA se designa con el prefijo D.
El aglutinante, que es el material de unión, tiene varias funciones, entre ellas la de evitar pérdidas prematuras de grano, permitir liberar granos desafilados, transmitir fuerzas entre grano y husillo y disipar el calor generado en el proceso.
Puede ser de un tipo u otro dependiendo de la aplicación y la resistencia requerida:
- Vitrificado: el más común en el mercado. Para rectificados de precisión
- Resinoide: no emplear cuando existen altas temperaturas ni con fluidos alcalinos
- Metálico: empleado con muelas de CBN y diamante, bajo desgaste, elevada retención de los granos, no son porosas
- Otros: de goma, elastómero, etc.
2. Parámetros claves en la selección de muelas
- Tamaño de grano: definido por la norma FEPA (existen otros estándares internacionales como ANSI, CAMI y JIS) un grano fino proporciona mejor acabado, mientras que uno grueso permite mayor remoción de material (desbaste) con un acabado superficial "pobre". Generalmente, en el proceso de rectificado se suelen usar grano de 30-100.

- Dureza o grado de la muela: es la resistencia del aglomerante a “soltar” granos como consecuencia de las fuerzas en el proceso. Representada por letras de la A (blanda) a la Z (dura). Las muelas blandas son idóneas para materiales duros, y las duras para materiales blandos.

- Estructura: indica la cantidad de porosidad y se designa con un número que indica el grado de “apertura” de la muela. Una muela más abierta permite mejor refrigeración y evacuación de virutas.
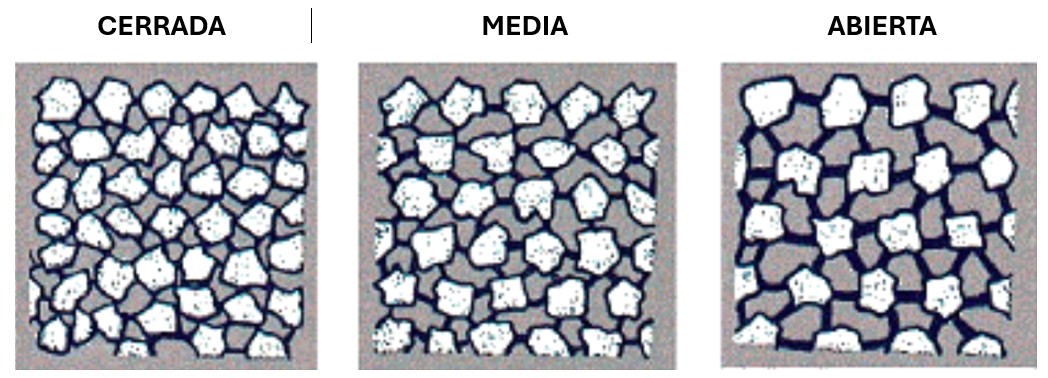
- Velocidad de rotación: hay dos velocidades que se deben considerar:
Velocidad periférica (m/s): Es la velocidad a la que se mueve la superficie de la muela en contacto con la pieza de trabajo. Debe ajustarse según el tipo de material que se está rectificando. En las rectificadoras sin centros, hay que distinguir la velocidad de la muela rectificadora o de trabajo y la de la muela reguladora o de arrastre (su velocidad es mucho menor y controla el avance de la pieza)
Velocidad de giro (rpm): Es la cantidad de revoluciones por minuto que realiza la muela. Está relacionada con el diámetro de la muela y la velocidad periférica.
Si la velocidad de rotación es demasiado baja, la muela puede desgastarse de manera irregular y perder eficiencia en la remoción de material. Si la velocidad es demasiado alta, la muela puede fracturarse debido a la fuerza centrífuga, lo que representa un gran riesgo de seguridad. Por eso, cada muela tiene un límite de velocidad máximo recomendado por el fabricante. Es fundamental usar una muela diseñada para soportar la velocidad de la máquina rectificadora.
- Propiedades térmicas y químicas: las muelas abrasivas deben poder disipar el calor de manera eficiente para evitar sobrecalentamiento y quemaduras en la pieza de trabajo. Algunas muelas contienen materiales como cerámica o abrasivos con mayor conductividad térmica para reducir la acumulación de calor. Además deben ser resistentes a la reacción con el material que están rectificando. A veces se le añaden aditivos o ligantes especiales para mejorar la resistencia a la corrosión y aumentar la vida útil.
DESIGNACIÓN DE LAS MUELAS SEGÚN SUS CARACTERÍSTICAS:
Los fabricantes de muelas, dependiendo de todas las características vistas hasta ahora, establecerán un código de 5 caracteres con las siglas del tipo de abrasivo, tamaño del grano, grado, estructura y aglomerante utilizado, como por ejemplo B30N5M:
✅ Abrasivo de CBN (Nitruro de Boro Cúbico)
✅ Grano 30 (medio-grueso)
✅ Dureza media-dura (N)
✅ Estructura cerrada (5)
✅ Aglutinante metálico (M)
Otro muela abrasiva podría ser esta: 508x160x304,8 SC 54.2KL9V - 50 m/s:
✅ Dimensiones: 508 mm (Øexterior) x 160 mm (ancho) x 304,8 mm (Øinterior)
✅ Tipo de abrasivo: Mezcla de carburo de silicio y óxido de aluminio (SCP)
✅ Tamaño del grano: 54 (medio-fino)
✅ Dureza: Media-dura (KL)
✅ Estructura: Semiabierta (9)
✅ Aglomerante: Vitrificado (V)
✅ Velocidad periférica: 50m/s
En algunos casos, los fabricantes pueden indicar también la geometría de la muela (la forma).
3. Formas de las muelas
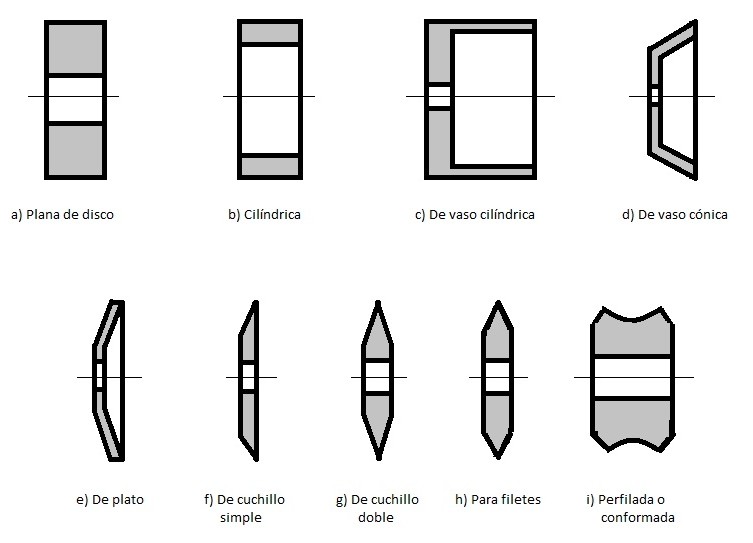
Existe una gran variedad de formas de muelas abrasivas para el rectificado, cada una con un uso específico.
A grandes rasgos, podemos decir que para rectificar superficies cilíndricas se emplean la a) y la b)
Para el rectificado plano se emplean las muelas de la forma c)
Para el afilado de herramientas se emplea la d)
Para afilar herramientas también y sierras se emplea la e)
Para desbardar fundiciones se emplean la f) y la g)
La h) como su nombre indica para rectificar filetes de roscas
Y finalmente la i) para rectificar perfiles o dar formas
4. Tipos de rectificado y posición de las muelas
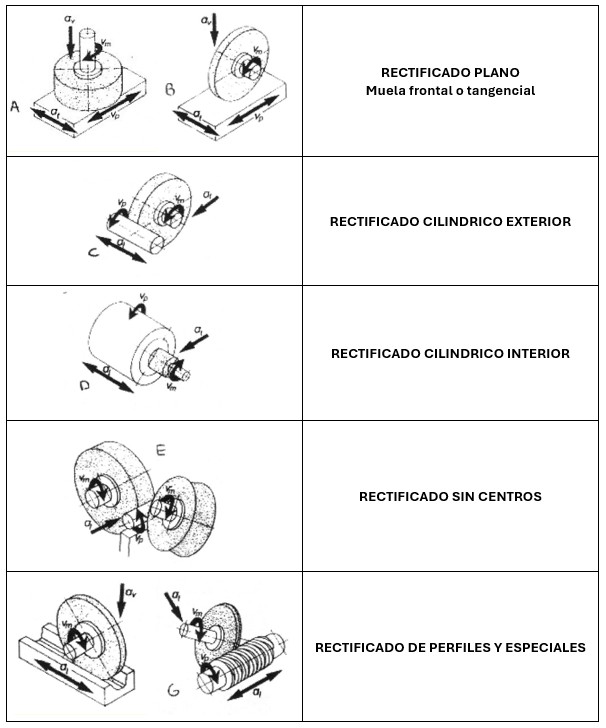
5. Movimientos de las muelas
- De corte (Mc): lo hace la muela de trabajo o rectificadora, independientemente del Mr´ y es del orden de los 2000 a los 2500 m/min
- De avance radial: la muela se acerca a la pieza para rectificarla
- De rotación (Mr): en el rectificado sin centros, la muela reguladora o de arrastre da el movimiento de avance a la pieza a rectificar. Es lento y comprendido entre 10 y 50 m/min
- Ángulo: es la inclinación que se le puede dar opcionalmente a la muela de arrastre, y que origina el desplazamiento axial de la pieza (cuanto mayor sea este ángulo, mayor será la velocidad del desplazamiento de la pieza a rectificar). Esta inclinación será aproximada de 1 a 5 grados.
- Avance axial (barrido lateral): en el rectificado cilíndrico, la muela se desplaza a lo largo de la pieza para rectificar toda su superficie
6. Montaje de las muelas
Para que el rectificado de una superficie con muelas abrasivas se haga correctamente, al montar la muela hay que tener en cuenta:
- El equilibrado de la muela: si no está bien equilibrada puede resultar en una mala calidad en la pieza, mayor desgaste de la muela y riesgo de fractura
- Sujeción de la misma en el eje portamuelas: una mala sujeción de la muela puede producir vibraciones excesivas, desviaciones en el rectificado, pérdida de precisión o incluso riesgo de rotura
- Diamantado de su superficie: si la muela no se diamanta correctamente se produce una reducción de la capacidad de corte, un acabado superficial deficiente, se generan fuerzas de rectificado más altas y un desgaste irregular
7. Diferencias de la abrasión respecto mecanizado convencional con herramientas de corte
- Las muelas, al contrario que en una herramienta de corte, disponen de un número indefinido de aristas cortantes, cada una de las cuales arranca una parte del material
- Los filos de corte se encuentran situados de manera aleatoria.
- Las virutas resultantes del proceso son de un tamaño mucho más pequeño.
- Las velocidades de corte pueden ser hasta diez veces superior a las que se pueden alcanzar con un mecanizado con una herramienta de un solo filo, debido a sus infinitos filos de corte.
- Es un proceso capaz de dar lugar a ángulos del plano de cizallamiento variables desde el inicio hasta el final del mecanizado, y permanentemente muy pequeños.
- La energía consumida en este tipo de mecanizado es muy superior a la de un proceso convencional, produciendo altas temperaturas tanto para la pieza como para la muela, pudiendo provocar quemaduras, grietas superficiales, tensiones residuales, modificaciones en la microestructura superficial y errores dimensionales. Por lo tanto, es imprescindible el uso de fluidos refrigerantes y lubricantes. Esta energía se distribuye en la mayor parte en la pieza, seguido a un nivel mucho más bajo por la herramienta y finalmente el resto de calor se lo lleva la viruta creada.
8. Mantenimiento y regeneración de muelas
Para garantizar la vida útil y la eficiencia de una muela, es esencial:
- Reavivado y perfilado: Se realiza con discos diamantados o herramientas de perfilado para restaurar la geometría de una muela desgastada.
- Control de velocidad y refrigeración: Evita sobrecalentamientos y deformaciones en la pieza.
- Almacenamiento adecuado: Las muelas deben guardarse en condiciones óptimas de humedad y temperatura para evitar su degradación.